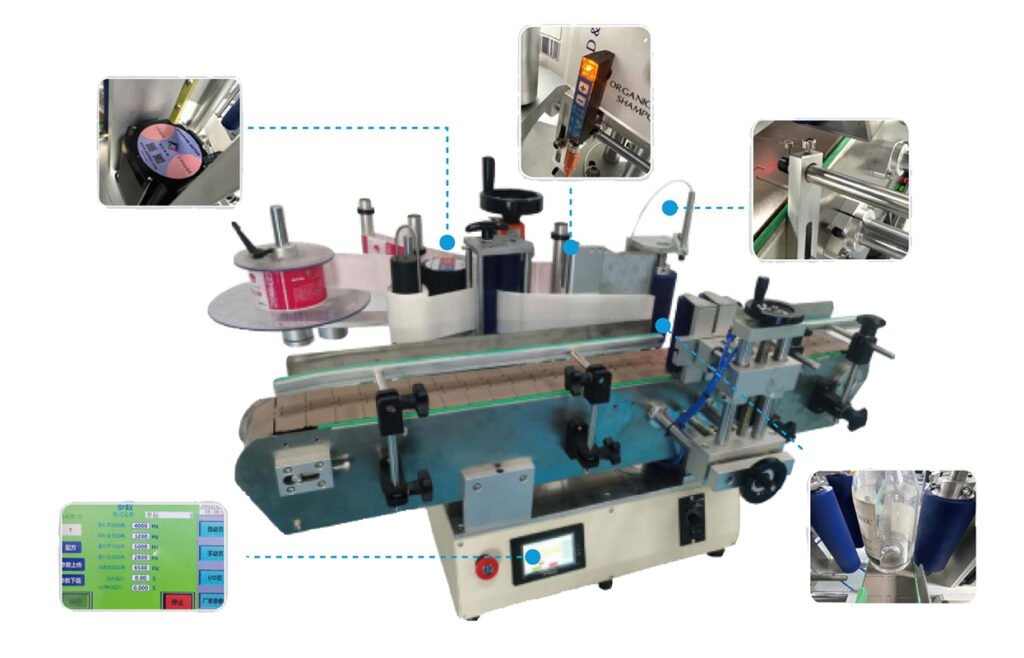
Tabletop labeling machines are invaluable assets for businesses seeking to streamline operations and enhance product presentation. However, like all machines, they occasionally encounter issues that can disrupt productivity and result in poor labeling quality. This guide provides a practical approach to diagnose and resolve the most common labeling problems, ensuring your machine operates efficiently and consistently delivers high-quality results.
Whether you’re facing label misalignment, jamming issues, or poor print quality, this step-by-step guide will help you troubleshoot and resolve problems quickly, minimizing downtime and maximizing productivity.
By the end of this guide, you’ll have the knowledge to confidently address any labeling challenges. Let’s dive into the essential steps for maintaining optimal performance with your tabletop labeling machine.
Initial Checks: Establishing a Solid Foundation Before Troubleshooting
Power and Setup: Verify Essential Connections
- Confirm Power Connection: Ensure the machine is plugged into a functioning power outlet and powered on.
- Check Power Supply: Confirm that the correct power adapter, as specified in the user manual, is being used.
- Consult the User Manual: Always refer to your machine’s user manual for specific model instructions and recommendations.
Supply Inspection: Confirm Material Compatibility and Loading
- Label Suitability: Verify that the label material, size, and adhesive are compatible with your product and machine specifications.
- Correct Loading Procedure: Load the labels properly, ensuring smooth unwinding and correct orientation.
- Label Supply: Check that you have enough labels and that the roll is not nearing depletion.
Ribbon (If Applicable): Inspect Ribbon Installation and Type
- Proper Ribbon Loading: Ensure the ribbon is installed correctly as per the manual, with the correct spindle placement and ribbon path.
- Ribbon Compatibility: Use the recommended ribbon type that matches the machine’s printhead technology.
Product: Ensure Product Compatibility and Condition
- Product Compatibility: Confirm the product’s size, shape, and surface type are suitable for the machine.
- Surface Cleanliness: Clean the product surface thoroughly to ensure proper adhesive bonding.
Problem-Specific Troubleshooting: Directly Addressing Labeling Issues
A. Label Skew and Misalignment: How to Straighten Crooked Labels?
Problem: Labels are applied at an angle, deviating from the straight line.
Causes:
- Label Guide Adjustment: Incorrect label guide settings lead to misalignment.
- Product Guide Adjustment: Improper positioning of the product guide leads to off-center feeding.
- Uneven Label Roll Tension: Inconsistent tension can cause the label to feed unevenly.
- Machine Leveling: An unleveled machine base can cause label skewing.
Resolution:
- Adjust Guides: Re-align the label and product guides to ensure a straight feed path.
- Tension Management: Ensure even tension on the label roll. Fine-tune for consistent feeding.
- Level the Machine: Use a level to check the machine’s position. Adjust feet for stability.
B. Label Feed and Jamming: How to Prevent Label Stoppages?
Problem: Labels become stuck, fail to advance, or cause machine jams.
Causes:
- Label Roll Tension: Too tight or too loose tension can disrupt the feeding process.
- Path Obstructions: Dust, adhesive residue, or debris in the label path can obstruct smooth movement.
- Static Electricity: Can cause labels to stick together.
- Label Stock Compatibility: Incompatible label materials cause feeding malfunctions.
Resolution:
- Tension Adjustment: Fine-tune the label roll tension for smooth advancement.
- Clear the Path: Inspect the entire label path for debris and clear it using recommended cleaning tools.
- Static Reduction: Use anti-static tools or increase ambient humidity to reduce static buildup.
- Verify Label Stock: Ensure the label stock matches the machine’s specifications.
C. Print Quality Degradation: How to Restore Clear and Consistent Printing?
Problem: Print appears faint, blurred, or incomplete, and smudges easily.
Causes:
- Print Density Settings: Low print density results in faded prints.
- Ribbon Supply: Low or incorrect ribbons cause poor print quality.
- Printhead Condition: Dirty or worn printheads lead to degraded prints.
- Material Incompatibility: Incorrect label and ribbon combinations can cause poor print adhesion.
Resolution:
- Adjust Print Density: Increase the print density settings for darker, clearer prints.
- Check Ribbon Supply: Replace ribbons if they’re low or improperly installed.
- Clean the Printhead: Regularly clean the printhead with isopropyl alcohol and lint-free cloths.
- Verify Compatibility: Ensure the ribbon and label stock are compatible for optimal print quality.
D. Label Adhesion Failure: How to Ensure Labels Stay Affixed?
Problem: Labels detach or peel off the product after application.
Causes:
- Contaminated Surface: Dust, oils, or moisture affect adhesion.
- Inappropriate Adhesive: The adhesive may not be suitable for the product or environment.
- Environmental Factors: Extreme temperatures or humidity interfere with adhesive performance.
- Insufficient Application Pressure: Inadequate pressure prevents proper adhesion.
Resolution:
- Clean the Surface: Ensure the product surface is free of contaminants and completely dry.
- Select the Right Adhesive: Choose an adhesive that matches the product material and environment.
- Control the Environment: Ensure temperature and humidity levels are optimal.
- Adjust Application Pressure: Increase application pressure for stronger adhesion if applicable.
E. Sensor and Detection Errors: How to Achieve Accurate Label Recognition?
Problem: The machine skips labels or fails to detect them correctly.
Causes:
- Sensor Mismatch: Incorrect sensor type selection in settings.
- Obstructions in the Sensor Path: Dust or debris can block the sensor.
- Inconsistent Label Design: Irregular gaps or marks on the labels cause detection errors.
- Label Material Properties: Transparent or reflective labels can confuse sensors.
Resolution:
- Verify Sensor Type: Ensure the correct sensor type (gap or mark) is selected.
- Clean the Sensor: Gently clean the sensor to remove dust and obstructions.
- Check Label Design: Ensure consistent label gaps or marks.
- Test Label Materials: Test with different label stocks to find one that works better with your sensor.
Advanced Troubleshooting and Professional Assistance
Software and Driver Considerations (For Computer-Connected Machines):
- Verify software compatibility and ensure the latest drivers are installed and configured correctly.
Consult the User Manual:
- For model-specific troubleshooting tips, error codes, and settings, always consult your user manual.
When to Seek Expert Help:
- If troubleshooting doesn’t resolve the issue or if there’s a hardware malfunction, contact the manufacturer or a qualified technician for assistance.
Preventative Maintenance: Ensuring Long-Term Performance
Establish a Cleaning Schedule:
- Regular cleaning prevents dust and adhesive buildup, extending machine life.
Proper Storage:
- Store the machine in a clean, dry environment to avoid damage from dust, extreme temperatures, and humidity.
Use Recommended Supplies:
- Only use manufacturer-approved labels and ribbons to avoid performance issues.
Review Settings Periodically:
- Regularly review machine settings to ensure they’re optimized for your current needs.
Conclusion: Achieving Reliable Labeling Results
By following the systematic troubleshooting steps outlined in this guide and committing to regular maintenance, you can ensure your tabletop labeling machine runs smoothly and consistently. By addressing issues early and effectively, you’ll maintain high-quality labeling results and minimize costly downtime.
Share your troubleshooting experiences in the comments below, or ask any questions you may have to contribute to our knowledge base. For additional support, refer to your user manual or contact the manufacturer directly.
By maintaining these best practices, you’ll continue to achieve professional, high-quality labeling with minimal interruptions.