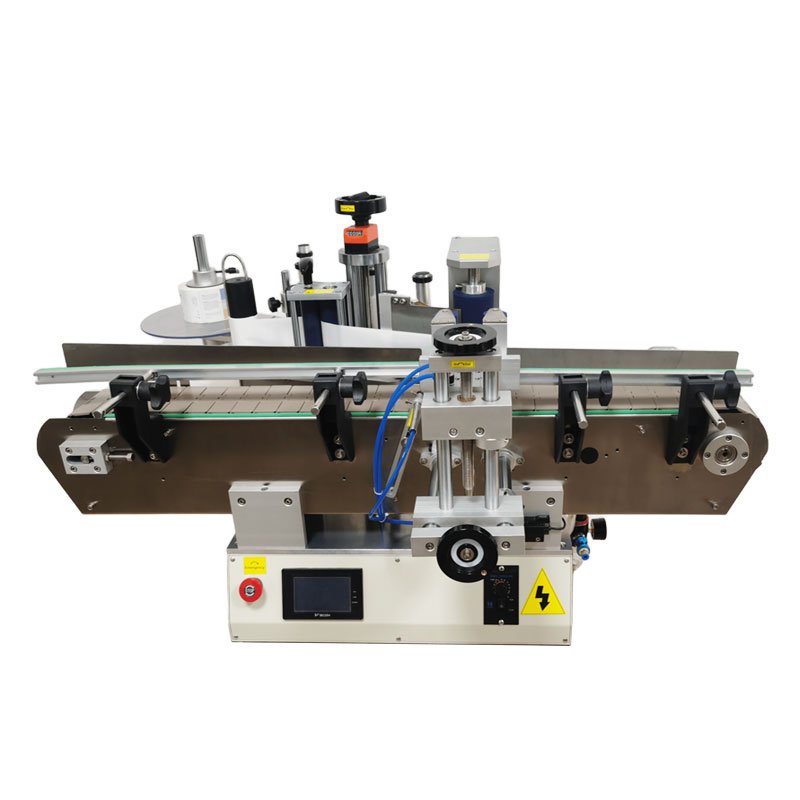
In the fast-paced world of product packaging, precision is non-negotiable. A tabletop labeling machine is a cornerstone of efficient operations, ensuring every product leaves your facility with a clean, professional, and accurately placed label. However, even the most advanced machine can falter if not set up correctly. Misaligned labels, adhesive failures, or sensor errors can lead to wasted materials, production delays, and dissatisfied customers. To avoid these pitfalls, a meticulous setup process is essential. This guide dives deep into the steps required to optimize your tabletop labeling machine for flawless performance, covering everything from machine selection to long-term maintenance.
Tips of Set Up A Tabletop Labeling for Better Accuracy
Choosing the Right Labeling Machine for Your Product
The journey to labeling accuracy begins long before the machine is powered on—it starts with selecting the right equipment for your specific needs. Tabletop labeling machines come in various configurations, each designed for different product types, label materials, and production volumes.
Understanding Product Requirements
- Container Shape and Size: Cylindrical products like bottles require wrap-around labeling systems that rotate the container as the label is applied. Flat-sided items, such as jars or boxes, need machines with front/back or top/bottom labeling capabilities. Irregular shapes, like tapered cosmetics bottles, may demand specialized applicators.
- Label Type: Paper, vinyl, foil, or clear labels each behave differently. For instance, clear labels often require optical sensors with high sensitivity to detect edges, while foil labels might need adjustable pressure settings to prevent wrinkling.
- Production Speed: High-volume operations (e.g., food or beverage industries) need machines with rapid cycle times and automatic feed systems. Lower-volume settings, like artisanal goods, may prioritize manual or semi-automatic models for flexibility.
Industry-Specific Considerations
- Food and Beverage: Machines with stainless steel components resist corrosion from moisture or cleaning agents.
- Pharmaceuticals: Look for systems compliant with Good Manufacturing Practices (GMP), featuring easy-to-clean surfaces and precision label placement for regulatory compliance.
- Cosmetics: Aesthetic precision is critical; machines with micro-adjustment capabilities ensure labels align perfectly with intricate bottle designs.
Key Features to Prioritize
- Adjustable Guides and Sensors: Accommodate varying product sizes and label positions.
- Digital Controls: Enable precise input of label dimensions, speed, and pressure settings.
- Modular Design: Allows upgrades, such as adding a printer for variable data labels.
Investing in the wrong machine risks frequent jams, misaligned labels, and costly downtime. Partnering with a reputable supplier like Simplabel ensures access to tailored solutions and expert guidance.
Preparing the Workstation for Optimal Setup
A well-organized workspace is the backbone of efficient labeling. Even minor oversights—like poor lighting or unstable surfaces—can derail accuracy.
Workspace Layout Best Practices
- Proximity to Packaging Line: Position the labeling machine near upstream processes (e.g., filling or capping) to streamline workflow. Ensure sufficient space for operators to load products and monitor output.
- Lighting: Install bright, shadow-free lighting to help operators detect label misalignments or adhesive issues.
- Stability: Secure the machine to a vibration-resistant surface. Use anti-slip mats or mounting brackets to prevent shifts during high-speed operation.
Pre-Setup Checklist
- Clean the Area: Remove dust, debris, or residual adhesive from previous runs.
- Organize Tools: Keep calibration tools, spare parts (e.g., rollers, blades), and label rolls within easy reach.
- Inspect Power Sources: Ensure electrical outlets meet the machine’s voltage requirements. Use surge protectors to safeguard sensitive electronics.
Ergonomics and Safety
- Adjust the machine’s height to reduce operator strain during loading.
- Install emergency stop buttons and ensure all safety guards are functional.
Adjusting the Labeling Parameters for Accuracy
Modern labeling machines offer extensive customization, but improper settings remain a common source of errors.
Step-by-Step Parameter Adjustment
- Label Placement:
- Use the machine’s digital interface to input label dimensions (length, width) and desired position (e.g., centered, 1 inch from the top).
- For irregular containers, manually adjust guide rails to keep products aligned on the conveyor.
- Conveyor Speed:
- Match the conveyor speed to your production rate. High speeds may require stronger adhesives or higher applicator pressure.
- Test incremental speed increases to identify the maximum rate without sacrificing accuracy.
- Applicator Pressure:
- Delicate labels (e.g., holographic) need gentle pressure to avoid tearing.
- For rigid containers, increase pressure to ensure adhesion on curved or textured surfaces.
- Environmental Factors:
- Temperature and humidity affect adhesive performance. Store labels in a climate-controlled area and adjust applicator settings seasonally.
Troubleshooting Common Issues
- Wrinkled Labels: Reduce applicator pressure or slow the conveyor.
- Peeling Edges: Increase pressure or switch to a stronger adhesive.
- Misalignment: Recalibrate sensors or tighten guide rails.
Calibrating the Label Sensors
Sensors are the “eyes” of your labeling machine, dictating when and where labels are applied. Even minor calibration errors can lead to skewed placements or missed labels.
Types of Sensors
- Optical Sensors: Use light beams to detect label gaps or notches. Ideal for clear or glossy labels.
- Mechanical Sensors: Physical brushes or levers that trigger labeling based on contact. Suitable for thick, opaque labels.
- Ultrasonic Sensors: Detect labels through sound waves, effective in dusty environments.
Calibration Process
- Manual Calibration:
- Align the sensor with the leading edge of the label.
- Adjust sensitivity settings to avoid false triggers (e.g., detecting gaps as labels).
- Automated Calibration:
- Many digital machines feature self-calibration modes. Input label specifications, and the system auto-adjusts sensor positions.
- Verification:
- Run a test batch and inspect labels for consistency. Adjust sensor angles or sensitivity as needed.
Pro Tips
- Clean sensors regularly with a microfiber cloth to prevent dust interference.
- Recalibrate when switching label materials or sizes.
Conducting Test Runs for Final Adjustment
Test runs are your final defense against labeling errors. They reveal issues that parameter adjustments alone might miss.
Comprehensive Testing Protocol
- Initial Batch: Run 10–20 products at low speed, inspecting each label for alignment, adhesion, and placement.
- Speed Ramp-Up: Gradually increase conveyor speed, monitoring for slippage or sensor lag.
- Edge Cases: Test with slightly oversized or undersized products to ensure guides and sensors accommodate tolerances.
Documentation
- Record optimal settings (speed, pressure, sensor positions) for future reference.
- Create a troubleshooting log to track recurring issues and solutions.
Case Study Example
A craft brewery struggled with labels peeling off chilled bottles. Test runs revealed that condensation disrupted adhesive bonding. By pre-drying bottles and switching to a waterproof adhesive, the issue was resolved.
Routine Maintenance Tips for Continued Accuracy
Consistent maintenance preserves precision and extends machine lifespan.
Daily Tasks
- Wipe down rollers, sensors, and conveyors to remove adhesive residue.
- Lubricate moving parts with manufacturer-approved oils.
Weekly/Monthly Tasks
- Inspect belts and gears for wear. Replace frayed belts or dull blades promptly.
- Check electrical connections and tighten loose components.
Long-Term Upkeep
- Schedule professional servicing annually for motor and software diagnostics.
- Update machine firmware to access the latest features and bug fixes.
Cost-Benefit of Maintenance
- A study by Packaging Digest found that proactive maintenance reduces downtime by up to 20% and cuts repair costs by 35%.
Conclusion
In an era where consumers judge products by their labels, accuracy is more than a technical requirement – it’s a brand imperative. A meticulously set up tabletop labeling machine ensures every product reflects your commitment to quality, compliance, and professionalism. By selecting the right equipment, optimizing workspace ergonomics, and adhering to rigorous testing and maintenance protocols, you transform labeling from a routine task into a strategic asset.
For businesses seeking to eliminate guesswork, Simplabel Machine offers end-to-end support, from machine selection to operator training. Contact us today to discover how our expertise can elevate your labeling process, reduce waste, and drive customer loyalty.